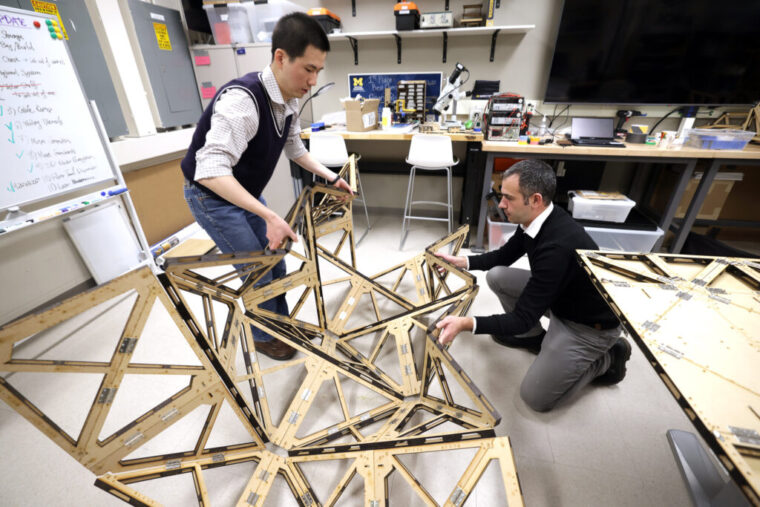
Researchers at the University of Michigan have shown how the principles behind origami can be used to create load-bearing structures such as bridges, walls, bus stops, columns and shelters.
Instead of using paper-thin components typical in traditional origami, the University of Michigan’s system utilizes thicker components that can fold into different shapes. The engineers combined this adaptive design with modular construction, in which structures are created off site and then transported to installation.
The system, known as the Modular and Uniformly Thick Origami-Inspired Structure system, could help communities rebuild facilities and infrastructure damaged or destroyed during natural disasters, researchers said.
Evgueni Filipov, an associate professor at UM and a member of the Deployable and Reconfigurable Structures Laboratory, said uniform thickness was the key to creating an origami structure that can support significant weight.
“What happens is you add one level of thickness here, and a different level of thickness there, and it becomes mismatched. So when the load is carried through these components, it starts to cause bending,” Filipov said. “That uniformity of the component’s thickness is what’s key and what’s missing from many current origami systems. When you have that, together with appropriate locking devices, the weight placed upon a structure can be evenly transferred throughout.”
Modular construction has been more widely adapted recently because of its time- and money-saving efficiency. Projects utilizing modular construction can take half as much time as traditional construction because both the foundation at the site and structures in the factory can be built simultaneously. Construction also isn’t delayed by weather or other uncontrollable circumstances.
UM engineers have been able to model multiple structure capabilities of the new system, utilizing a simulator called Sequentially Working Origami Multi-Physics Simulator (SWOMPS), which can predict the behavior of large-scale origami. The simulator was also developed at UM and has been publicly available since 2020.
So far, the team has demonstrated a 3.3-foot column that can support 2.1 tons of weight and a 1.6-foot cube that can unfold into a 13-foot-long walking bridge, a 6.5-foot-tall bus stop and a 13-foot-tall column. These demonstrations can translate into structures that can be assembled and disassembled for concerts or other events as well as emergency structures in case of natural disasters.
“With both the adaptability and load-carrying capability, our system can build structures that can be used in modern construction,” said Filipov, a corresponding author of a study on the system published in Nature Communications.
The project is funded by the National Science Foundation (NSF), a UM partner, and the Automotive Research Center.
Photo courtesy of the University of Michigan
The post Origami module shown to create load-bearing infrastructure appeared first on Government Market News.